Soflex
Soflex Overview
The Soflex flexible panel combines our unique base layer manufacturing process with our LTX Flexible Backer to create a highly flexible and extremely stable base layer that allows for fast and easy attachment of high-pressure laminates, veneers, metals and many other semirigid materials. When using Soflex, the decorative surfacing material can be applied while flat and then formed into the desired shape achieving a 3 1/2″ radius.
SOFLEX BENEFITS
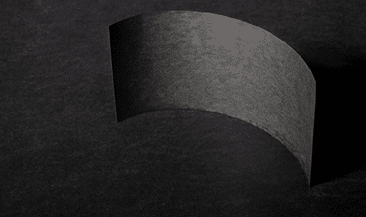
LTX Flexible Backer
Achieve a 3 1/2″ bending radius and virtually any shape you can imagine! Ideal for projects with complex curves.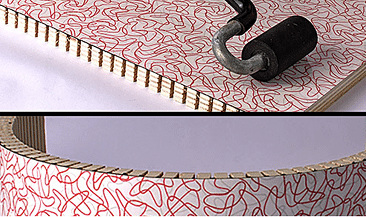
Laminate Then Form
Flat Lamination = fast consistent process. It is much easier to position the laminate and machine while flat than to laminate and machine a curved surface. Ideal for highly quality, consistently repeatable processes.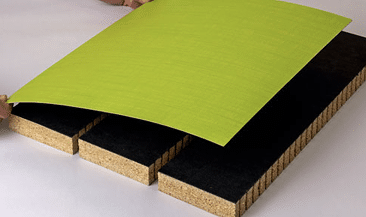
Easy-Splice
Eliminate scrap and use 100% of the material, by easily splicing in length or width to use small pieces to make larger and/or unique sizes.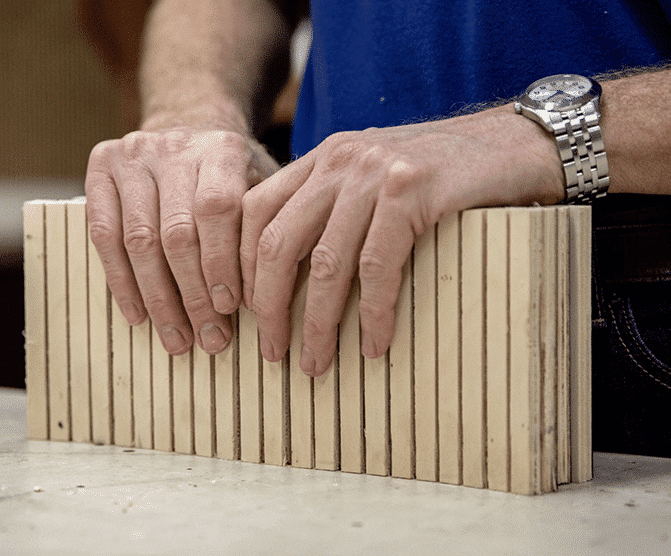
TECHNICAL OVERVIEW
Face Materials
LTX Flexible BackerCore Materials
Particleboard (Standard)Plywood
MDF
NAUF Particleboard
DOWNLOAD SPEC SHEET
SOFLEX FAQS
LTX Flexible Backer
Laminates should be applied to Soflex while flat and then formed into shape.
- Size Soflex to the desired finished dimensions.
- Apply the face material using a water or solvent based contact adhesive or a standard PVA glue (not a cross linking type).
- Allow glue to fully dry according to manufacturers recommendations.
- Use a router to easily trim the face material to match the finished size.
What face material is recommended for use on Soflex?
Best Options:
- High-Pressure Laminates (HPL)
- 20 Mil Paper Backed Veneers
- Phenolic Backed Veneers
- Two-Ply Veneers
- Metals
- Other similar bendable materials most likely will work, but a small test should be done before proceeding on bigger projects.
How do I attach Soflex flexible panels to a framework?
Soflex’s flat lamination process makes it easy to cut grooves or dados into the back of the base material, allowing it to easily fit over or against forming ribs. The grooves and ribs can be attached using a PVA glue and pins. Use a hot melt glue to help secure the parts until the PVA glue can cure. If you prefer not to cut grooves or dados, Soflex can be glued together and then clamped into place.Can Soflex be used to make curved doors?
Laminates should be applied to Soflex while flat and then formed into shape.- Size Soflex to the desired finished dimensions.
- Apply the face material using a water or solvent based contact adhesive or a standard PVA glue (not a cross linking type).
- Allow glue to fully dry according to manufacturers recommendations.
- Use a router to easily trim the face material to match the finished size.
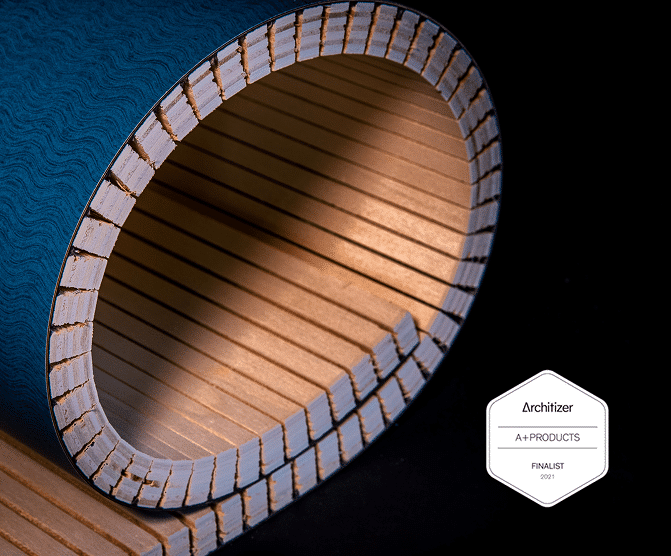
PRODUCT TESTIMONIAL
"In using Soflex products, I find it has saved me in time and labor over traditional methods. It gives me a consistent result every time. It also has expanded our ability to be creative for the customer."Roger Smith | Third Day Creations
REQUEST A SAMPLE