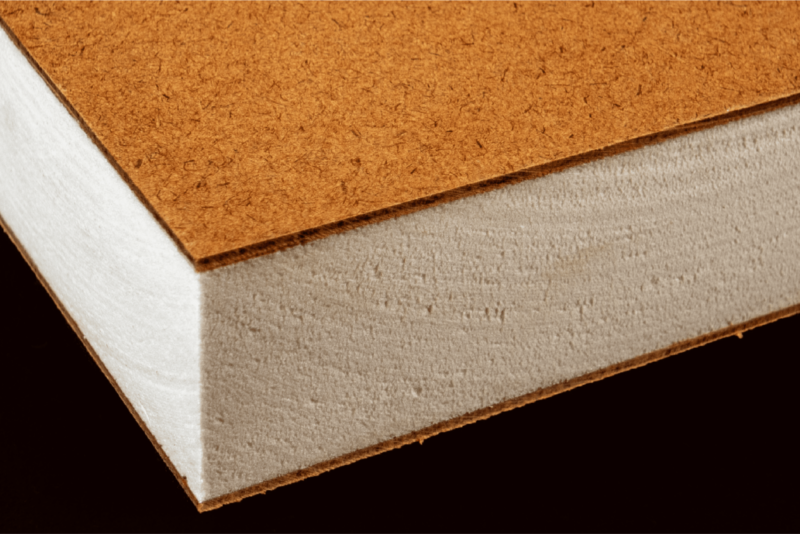
Worklite XPS Foamkore Benefits & Color Update
February 13, 2024In the culinary world, every incredible recipe has a secret ingredient or a special sauce that makes it memorable. Rather than a secret sauce, what separates our line of sandwich panels a.k.a Worklite Panels is their signature Extruded (XPS) and Expanded (EPS) Polystyrene Cores. While they are the “meat” of our Worklite Panels, these core ingredients aren’t developed in the kitchen, instead, they’re created through a chemical manufacturing process that gives each core its unique flavor…or properties. (Please do not taste any Worklite Panels.)
EPS Foam vs. XPS Foam
So, what’s the difference between the two materials used in our lightweight Worklite Panels?
EPS is known as a dense closed-cell foam structure, created during manufacturing as the foam is made from expanding polystyrene beads with steam, then bonding the beads under pressure.
XPS is also a closed-cell foam and its manufacturing process begins with the same materials as EPS but is fed additives and expands during cooling. This process allows for very smooth edges.
Both XPS and EPS have plenty of use cases in the world of architecture but today we will be focusing on XPS foam as there are some colorful changes ahead.
Worklite XPS Foamkore® Foam Changing from Blue to Grey
If you’ve ever worked with our Worklite XPS Foamkore®, you’ve likely noticed the bright blue foam. In the coming months, that foam will be transitioning from blue to grey. While the team here at Kerfkore will miss that pop of blue around the office and factory, according to DuPont™, the new grey foam will have less global warming potential without sacrificing performance.
So, if you receive a shipment of Worklite XPS Foamkore and see the grey foam instead of blue, fear not! Worklite XPS Foamkore will still be lightweight, easy to work with, and perfect for projects that involve any of the three Os — Oversized (think large door panels), Overhead (for decorative ceilings or hanging baffles), or Overweight (RVs or tradeshow displays). The color shift will be transitionary, so it is entirely possible to receive either the grey foam or the blue in the coming months. Diehard Kerfkore fans might want to hold on to the blue Worklite XPS Foamkore as a collector’s item!
Why Use Foam in Sandwich Panels?
All of this foam talk may have you wondering why we use it in the first place. Well, unlike our flexible architectural panels which are designed to offer a rare combination of dynamic, curvy, and sturdy designs — our Worklite XPS Foamkore panels are focused on being light, strong, and as easy to work with as possible.
Reduces Material Weight by up to 80%
When compared to conventional panels made of plywood, particleboard, and medium-density fiberboard.
Moisture Resistance
Thanks to the XPS closed-cell structure, it has great moisture resistance compared to other foam products.
Easily Customizable
XPS foam makes the Worklite XPS Foamkore easily customizable as it can be cut to a smaller size or extended to meet special orders by our customers. We can also press a laminate, veneer, metal, leather, or similar semirigid materials and add custom frames and internal bands. All of these customization options save customers time and resources. Speaking of Kerfkore customization capabilities saving customers time and resources, below is a custom door project that was built using Worklite XPS Foamkore.
Worklite XPS Foamkore in Action
Earlier we mentioned how Worklite is great for the three Os. Check out how Worklite XPS Foamkore was used for a custom-built oversized door.
Step 1
First, before the XPS foam was incorporated, the finger-jointed poplar (FJP) wood used for the door panels was sanded to become the appropriate (over)size.
Step 2
Then our Kerfkore team cut the FJP wood to the various sizes needed for the project, organized for maximum efficiency.
Step 3
The door panels were then assembled to the specifications provided by the customer.
Step 4
Now, for the foam. The XPS foam was cut to size with a panel saw so it was able to fit snuggly within each panel.
Step 5
Before application, the face materials were sent through our glue spreader to spread a precise amount of PVA glue. Then the face materials were placed on both sides of the panel to cover the internal XPS foam and framing.
We offer three different face materials for paneling:
- Eucalyptus Hardboard
- Fiberboard
- 3-Ply Italian Poplar Plywood
Typically, we recommend Fiberboard or 3-Ply Italian Poplar Plywood for your door’s panel face material (if there is internal banding and framing) to ensure no telegraphing. The material shown in the picture is 1/8″ Fiberboard.
Step 6
Then, with the help of our press machine, the face materials were further adhered to the XPS Foamkore materials. The press machine is set to a precise PSI for a specific amount of time to ensure the face materials are firmly attached to the core and frame without overpressing. Thanks to XPS foam’s compressive strength, it’s able to withstand the pressure from the press machine, providing robust adhesion properties.
Step 7
After the face materials of the panel were firmly adhered to the core, the process of drying the panels began. Elevation rods were placed in between each stacked panel, which allowed even airflow on each side.
The panels were then placed in a humidity-controlled room for 24 hours, to ensure there was minimal moisture. This not only reduces the weight of the panel but ensures that our panels will not warp and will stay lightweight and maintain their aesthetically pleasing look for years.
Step 8
Once the panels were completely dry, they were taken to a panel saw for trimming and cleanup. This step ensured face materials were flush and perfectly aligned with the framing so that the edges were neat, clean, and smooth.
Step 9
Finally, the custom door panels were packaged for shipment. The lightweight Worklite XPS Foamkore not only makes a fabricator’s job easier but also makes shipment easier compared to heavier materials.
You can read more about these custom door panels here. Or if you’d like to find out how Kerfkore can help you with a custom project, contact us today.
XPS Foam is Our Secret to Staying Light
Whether it’s blue or grey, the foam that makes up the core of our incredibly lightweight, yet strong Worklite XPS Foamkore will continue to help you reimagine what’s possible for your next architectural or fabrication project. To see it in action, request a free sample today. Until then, check out even more information about our Worklite XPS Foamkore product here.
Editor’s Note: In this blog post, we have referenced products and company names to provide comprehensive information to our readers. We want to explicitly acknowledge that DuPont™ and their respective product names mentioned herein are registered trademarks or trademarks of DuPont™. These trademarks are the property of their respective owners, and we do not claim any affiliation or endorsement by DuPont™.