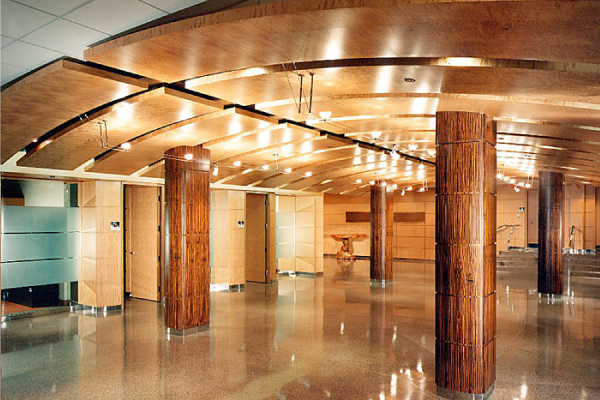
Types of Curves in Architecture and Woodworking
March 21, 2022From the arches of the Roman Colosseum to the Gateway Arch of St. Louis, curves have attracted architects for thousands of years for their unique combination of supporting strength and inviting aesthetic.
Curves have even bled into software and tech design. Apple, makers of the curved-edged iPhone, are lauded for their user-friendly design and insist on eschewing the precise squares and edges that once dominated computers and other tech designs.
Like a tree branch or a blade of grass gently curving downward, Apple understands that the organic feeling of a curve makes it easy for their products to be picked up and hard for them to be put down.
That same natural feeling can be applied to interior design, where an area with relaxed curves is a much more inviting space than an area with hard edges, especially when paired with organic materials like wood.
Curved Wood Designs: Concave and Convex
At Kerfkore, our specialty is creating curves with wood and when it comes to discussing designs, we should start with the two most basic types of curves: concave and convex. Both have a wide range of applicable uses and can achieve the strength and welcoming aesthetic arches and curves are known for.
What is the difference between concave and convex?
Concave describes a curve that bends inward, like a cave or the inside of a bowl. Convex describes a curve that bends outward, such as the outside of a bowl.
Different Types of Curves
While convex and concave describe which way a curve is bending, there are multiple types of shapes that can be created by combining convex and concave curves. Understanding the basic types of curves can help architects and fabricators achieve unique and welcoming designs.
Circular – a simple circular curve, which can be closed or c-shaped
Curvilinear – a line of curves, normally cresting and dipping
S Curve – as the name implies, a curve, shaped like the letter S
Spiral Curve – a circular curve that continues wrapping around with tighter and tighter circular curves
Tilde Curve – a small curve that dips at the beginning and points up at the end, used as an accent symbol
These curves vary in complexity and as such, they can vary in how difficult it can be to apply to wood. A tilde curve, for example, can be created very easily as it only requires two curves to be created in the wood paneling but a spiral curve is a continuous series of curves which makes it inherently more complex.
How can you bend wood?
In order to create simple or complex wood curves, we first need to determine which process we should use for bending the wood. Bending wood to either a convex or concave curve can be achieved by one of the four following methods: bendable plywood, steam bending, self kerfing, and engineered materials.
Bendable Plywood
Bendable plywood, like normal plywood, consists of several thin wood layers or plies glued together. It can be obtained in various ranges of size and thickness but in general, it is relatively thin compared to other plywoods to achieve flexibility. Unfortunately, the same properties that make it flexible also make it less durable. As such, bendable plywood’s uses are limited to projects that don’t demand a lot of durability from their materials.
Steam Bending
Steam bending refers to the process of softening wood with steam until it becomes pliable. The science behind steam bending works like this: the wood cells are comprised of Lignin, which makes wood, well woody (i.e. rigid), and cellulose fibers – the plant fiber. Steam heats the Lignin until it becomes liquid, which allows the cellulose fibers to be repositioned.
Steam bending is a unique process but it can leave the wood prone to eventually returning to its original form which could be potentially disastrous for projects with aspirations of longevity. It also demands the user know the exact specifications of how their wood will fit into the project as it can’t be adjusted while attaching.
Self-Kerfing
Self-kerfing refers to the process of manually making many small, equally spaced incisions into the wood until it becomes bendable, then attaching a backing to the wood so it can maintain its shape. Self-kerfing is very time-consuming, a bit tedious, and doesn’t always yield a perfect design but when done correctly can create a very flexible wood that can be used to create a variety of curves.
Engineered Wood
Engineered wood materials, meaning manufactured wood products like Kerfkore, can circumvent the issues of hand-making your kerfs. Instead of pouring time and resources into a project that may or may not turn out as desired, you can rely on machine precision and consistency. While some fabricators may want to self-kerf to achieve a certain size or bend radius, Kerfkore offers custom options to fit a huge range of projects.
For projects that want to achieve curves or arches with the precision of a machine but an aesthetic fit for a museum, engineered materials like Kerfkore are unparalleled.
No matter the method or material used – curves and arches have long been an integral part of some of the most famous and celebrated architectural designs in history. At Kerfkore, we value the warm spaces our wood panels can provide but we remain excited for any of the possibilities that the future of architecture holds for our favorite shape.
Feeling inspired to incorporate curves into your next architectural or interior design project? We offer a variety of flexible panels with a range of maximum bending radii so you can build your next architectural or interior design project with a natural, warm, and inviting look. Download our Flexible Guide to see our full range of options.